Introduction to actuating materials
Devices that produce forces and displacements are known as "actuators"[1]. Electric motors and combustion engines are type of actuators that we are probably the most familiar with. They rotate and produce torque when they are supplied with electricity, powering up our transportation systems and mechanical devices that our lives depend upon. However, you are probably unaware of the fact that one of the most powerful actuators exist within our bodies - human skeletal muscles [1]. These muscles come in units of bundles of muscle fibres, which contract upon receiving actuation signals transmitted from the brain to the muscle units via neurons. The actuation of muscle fibres enable us to perform all types of complex movements.
This page provides a brief introduction to existing types of actuating materials, their working principles and typical applications. A larger proportion of this page is devoted to the explanation of nanoporous metal actuators since it is the most relevant to the work of our research group.
Piezoelectric actuators
Working principle
Piezoelectric materials are certain types of ceramics that exhibit "direct piezoelectric effect" and "indirect piezoelectric effect". Direct piezoelectric effect refers to the ability to generate electrical charges proportional to material's deformation; indirect piezoelectric effect refers to the opposite: the stress develops in the material when an external electric field is applied [3]. Force sensors often employs the direct piezoelectric effect of piezoelectric materials. When piezoceramics are used as artificial muscles, a high electric field is applied to the material (typically > 1kV) which cause the dipoles in the material to align thereby introducing a small change in length, denoted as actuation.
Characteristics
Piezoceramics are capable of high frequency actuation and generation of high actuation stress (several tens of MPa), which compensates for its small strain and yields a high mechanical work density. The main limitations of piezoelectric actuators are the high electric field required and low strain (typically 0.1%). Strain amplification mechanisms are often required by piezoelectric actuators which increases the space occupied by the actuator unit.
​
​
Applications
One example is the quartz in the wristwatch. The battery in the wristwatch applies certain electric field to the quartz causing it to vibrate, where a micro-chip inside the watch counts the number of vibrations and ticks every time a certain number has been accumulated. Other applications include precision-positioning devices such as ink-jet printing heads, strain gauges, microphones, speakers, and micro-actuators for hard disks and notebook transformers.​​
Electroactive polymers (EAPs)
Polymers that exhibit dimensional changes in response to electric stimulus are called electroactive polymers (EAPs). EAPs are classified according to whether the actuation is facilitated by Columb force caused by an external electric field, or diffusion of electrolytes caused by gradients of ionic species. The former type of EAPs are electronic EAPs, whereas the latter type are ionic EAPs. Common electronic EAPs include dielectric elastomers, and common ionic EAPs include ionic polymer gels, ionic metal/polymer composites (IPMCs), and conducting polymers (CPs).
Working principle
Dielectric elastomer actuators consist of two thin metal electrodes and a dielectric medium in between. The dielectric medium are often incompressible but deformable elastomeric materials. When a high external electric field is applied (typically requiring > 150 MV/m), static charges appear at both metal electrodes and the attraction force between the charges (Columb force) deforms the elastomer.
Dielectric elastomers
Characteristics
Dielectric elastomers are appealing actuators because they possess large strain, large work density, wide actuation frequency range (10 Hz - 1 kHz), good energy efficiency (>15% electromechanical coupling), low costs, and low current consumption (despite the fact that voltage requirement is high) [1]. The video on the left shows a linear actuator made of dielectric elastomer developed at Empa - Material Science and Technology - Switzerland.

Ionic Metal/Polymer Composites (IPMCs)
Working principle
Ionic polymer metal composites (IPMCs) typically consist of two thin metal electrodes sandwiching an ionic polymer layer that is (often) negatively charged. The polymer is mixed with solvents containing mobile cations to equalize the negative charges in the polymer. When an electric field is applied across the metal electrodes, the cations are attracted to cathode and its movement are accompanied by the movement of the solvent (e.g. water), causing expansion in IPMC towards the direction of cathode. Immediately after this, the pressure in the strained polymer causes water to diffuse away from the cathode, resulting in slow relaxation of IPMC back to its original position.
Applications
IPMCs have been used as propellers in many underwater robots projects due to its flexibility, large actuation strain, and low actuation voltage. IPMCs can mimic both undulatory and oscillatory swimming motion of fish. The video on the left shows a biomimetic robotic ray propelled by series of IPMC actuators on each side of robot to imitate the sinusoidal waveform of ray's fin, jointly developed by The University of Tartu and Tallinn University of Technology. The video on the right shows IPMC as an oscillatory tail propeller developed at The University of Nevada.
Characteristics
The main advantages of IPMCs are low actuation voltages (typically < 10V), large actuation strain (~3.3%) as a result of hydrophilic expansion, and relatively low cost to produce (compared to nanoporous metals and carbon nanotubes). The drawback of IPMCs is the complex encapsulation required to avoid the solvent loss during actuation. Also, current IPMCs feature a low electromechanical coupling (~3%) and efficiency (<3%). [1]
Conducting Polymers (CPs)
Working principle
Conducting polymers (CPs) are also known as "conjugated polymer". These are electronically organic materials featuring different conjugate structures. There are two dominant actuation mechanisms in CPs. The first mechanism is similar to that in IPMCs: when an external electric field is applied to the polymers, the polymer oxidizes and results in addition or removal of charges from the polymer backbones. This attracts a flux of ions within the electrolyte to balance the charge, and the diffusion of ions are accompanied by the movement of solvent, resulting in reversible swelling in the actuator. The second actuation mechanism arises from conformational changes in polymer backbones [1]. Several species of polymers undergo rotation, folding, or exhibit different staggering arrangements when electrochemically switched to different conjugated structures, thereby introducing a difference in length.
​
Characteristics
CPs feature high strengths (Young's Modulus as high as 3 GPa) and stiffnesses, large actuation stresses (maximum 34 MPa), and low actuation voltages (typically 1-2V). However, its strain is relatively low (~2%) and the actuation rates are limited by the resistance and ion transport speed within the polymers [1].
​​
Applications
CPs have been applied in braille cells and variable camber actuators. Due to their high degree of biocompatibility, CPs have also been employed in biomedical devices [1]. Recently, McGovern et. al and Fay et. al used CPs as underwater propellers in their robotic fish project. The following video shows their work.
Source: http://www.youtube.com/watch?v=Ga_IafGRWyE, which includes--
NEMO (Novel Electrochemical Muscle Oscillator) project:
McGovern ST, Alici G, Truong VT, Spinks G. 2008. Fast bender actuators for fish-like aquatic robots. Proc. of SPIE Vol. 6927, 69271L,
​
WANDA (Wireless aquatic navigator for detection and analysis) project:
Fay C, Lau K, Bierne S, Conaire CO, McGuinness K, Corcoran B, O'Connor NE, Diamond D, McGovern S,Coleman G, Shepherd RL, Alici G, Spinks G, Wallace G. 2010. Wireless aquatic navigator for detection and analysis (WANDA). Sensors and Actuators B, 150: 425-435.
​
Source:https://youtu.be/hDpWPZTGjeU
Source:
http://www.youtube.com/watch?v=ccaJKascw8E
​
Original publication:
Punning, A.; Anton, M.; Kruusmaa, M.; Aabloo, A. 2004. A Biologically Inspired Ray-like Underwater Robot with Electroactive Polymer Pectoral Fins. IEEE Confrence "Mechatronics and Robotics 2004, 2:241 - 245.
Source: Kam K. Leang, the Electroactive Systems and Controls Lab (easyLab) at the University of Nevada
​
The loss of water results in reduced cell pressure, causing the cells to collapse and leaving the leaves shut. Here, the chemicals released by pulvinus is considered as the stimuli, and the loss of turgor pressure is the actuation mechansim.
​
"Artificial muscles" are actuating materials which mimic the properties of skeletal muscles, capable of generating forces and displacements when stimulated by voltages, magnetic fields, light, or temperature differences. Unlike traditional actuators such as motors, hydraulic or pneumatic actuators, which require additional components (such as gearboxes, linkages, hinges) to couple and deliver the mechanical work, artificial muscles can actuate themselves thereby saving a lot of space.
​
The application of artificial muscles are beyond imaginations: they play a significant role in robotics (especially soft robotics) and miniature mechanical systems such as MEMS (micro-electronic mechanical systems) and lab-on-a-chip devices [2]. They are sometimes utilized as sensors and generators. In biomedical applications, they can be deployed for fluid filtration, living cell manipulation, and minimally invasive surgical or diagnostic tools [1].
​
The following is a basic introduction to common types of actuating materials and its applications. For more detailed explanations of the materials, one is suggested to read the publications by Madden et. al [1] and Detsi et. al [2].
Another type of actuator that you probably have come across is mimosa pudica. Remember the first time in your childhood when you stared in awe at the plant when the foilages suddenly closes when you touch them? The secret to the rapid movement of mimosa pudica is that when its receptor senses touches or shaking movements, the swollen base of the leaf stalk ('pulvinus') releases various chemicals, building up a chemical concentration gradient that causes the water/electrolyte to diffuse out of the plant cells.
Shape memory alloys (SMAs)
Working principle
Shape memory alloys (SMAs) are one type of commercially available actuators along with piezoceramics and magnetostrictive materials. SMAs, as its name implies, exhibits "shape memory effect". This refers to the phenomenon as following: if we apply certain stress to SMAs at its austenized state, the austenite transforms into deformed martensite phase (twinned martensite), during which residual stress builds up in the material. When the SMA is reheated above the austenitic temperature, SMA returns to its original shape while being in the austenitic phase and releases the residual stress accumulated in previous stage, hence denoted as "shape memory effect" [4].
actuation stress (several hundreds of MPa) and unmatched work density (1 MJ/m^(3)). Moreover, a strain rate as high as 300%/s can be achieved by using very large current pulses and water cooling, with which the contraction can be shortened to several milliseconds. [1] This strain rate is even higher than some piezoelectric actuators (usually >10%/s).
Applications
Shape memory alloys enjoy wide range of applications including biomedical reinforcement devices, fire protection lines, eyeglass frames, and helicopter blades. [5]
The high temperatures to induce phase transformation in SMAs are normally achieved by resistive heating where a high current is passed through a thin alloy wire. The contraction time of the actuators is governed by the speed at which phase transformation occurs, and is thus dependent on the rate of heating and cooling of the alloy.
​
Characteristics
SMAs is a powerful actuating material due to several reasons: it generate moderate strain (typically ~ 5%) and it is capable of high
Nanoporous metals
Nanoporous metal actuators is a relatively new category of actuating material which is still under intensive research. Nanoporous metals are characterized by a high surface-to-volume ratio with its nanoporous structure synthesized from de-alloying method. Unlike the actuators introduced above, a nanoporous metal actuator must operate in a wet environment, i.e. in an electrochemical cells containing electrolyte, since its actuation mechanism relies on electric charge transport by ions.
​
Typical nanoporous metal actuators include:
-
Alloy types: np –Au, np-Ag, np-Cu, np-Py, np –Pd, np-Ni, polymer decorated np-Au composites (np = nanoporous)
-
Nanostructure types: nanowires, nanohoneycomb, nanotubes
Actuation mechanisms
​
Charging/discharging of capacitive electrochemical-double-layer (EDL)
When an external voltage is applied to nanoporous metals, ions with positive or negative charges in the electrolyte are attracted to the metal's surface and this affects the distribution of the surface free electrons of metal electrode. This enhances or weakens the strength of interatomic bonds at the surface layer of the nanoporous metal, thereby inducing an increase/decrease in surface stress. Stress with opposite direction is then induced in the bulk to achieve equilibrium. Consequently, the bulk expands/contracts according to the surface stress state. [2] The ionic charges attracted to the actuator's surface is of opposite sign to the free electrons at the actuator's surface, and since there is no charge transfer between actuator and the electrolyte just like charges at the two electrodes in a capacitor, these pair of charges are sometimes called the "capacitive electrochemical-double-layer (EDL)" which locates at the metal/electrolyte interface.
​
Noted that the above actuation mechanism is not significant in bulk metals but is important in nanoporous metals since the large surface area dominates the material's behavior. Thus, the smaller the ligament diameter of the nanoporous structure, the greater the actuation strain due to larger surface area for actuation. The reason why Au and Pt are suitable metals for nanoporous actuators is due to their small accessible ligament sizes (< 10 nm) compared to other metals such as Ag, Ni, Cu, which is advantageous for generating larger actuation strain.
​
​
Redox reaction
Except precious metals such as Ag, Pt which are highly stable against acids or alkalines, it is often impossible to preserve a "clean" metal surface during the actuation of nonprecious nanoporous metals since the metal reacts with the electrolyte. The actuation mechanism is then not only induced by the stored surface charges, but also through the charge transfer between electrolyte and the reaction product of metal with the electrolyte. For example, thin layers of nickel hydroxide were found to form at the surface of nanoporous nickel when it was actuated in 1 M sodium hydroxide solution (NaOH). The major actuation strain was attributed to the volumetric changes in nickel hydroxide layer induced by electrochemical reaction of Ni(OH)2 <-> NiOOH.
Unlike in the EDL mechanism, where the strain is linearly proportional to the amount of charge stored at the actuator's surface controlled by the externally applied voltage, the strain due to redox reaction is not proportional to the applied potential. Only a certain potential is required to "activate" the redox reaction (to overcome chemical energy barrier), and once the chemical energy barrier has been overcome, the maximum amount of strain that can be produced is limited by the difference in unit lattice constant between nickel hydroxide and nickel oxyhydroxide. The strain also decreases at higher actuation frequencies due to insufficient time allowed for ions to diffuse to the nanoporous surface, leading to incomplete redox reactions. Whereas the strain due to EDL mechanism was relatively constant from low to high actuation rate.
​
Applications
Nanoporous metals are pronounced energy storage materials and have been intensively used in fuel cells, catalysts, and sensors. Due to the limited strain nanoporous metals can provide, its usage as mechanical actuators are still under investigation.
Carbon Nanotubes (CNTs)
One may recall the space escalator project claiming to bring human to the moon via carbon nanotube cables. Carbon nanotubes possess extraordinary high stiffness at the macroscopic scale. It is less well-known that they are also powerful artificial muscles when synthesized at smaller length-scales.
Carbon nanotubes (CNTs) are graphite sheets rolled up into cylinders with diameters of the order of a few nanometers and up to some millimeters in length with at least one end capped with a hemisphere of the fullerene structure (C60). These tubes are either conductive or semi-conductive, therefore having some degrees of metallic properties. Due to Van der Waal's forces, the nanotubes tend to aggregate in bundles with a typical diameter of ~ 10 nm. [1]
CNTs need to be actuated in electrolytes. The actuation mechanism in CNT lies in the charging/discharging of electric-double-layer (EDL) to induce surface stress difference, the same mechanism as in nanoporous metal. When voltage is applied to the CNT, ions in the electrolyte are attracted to the actuator, inducing redistribution of the free electrons at the graphite's surfaces. This generates changes in surface stress, which cuases bulk volume contraction/expansion. However, the EDL is destroyed at a high voltage-- the high electric field causes breakdown of the EDL, where the ion solution began to exchange electrons with the nanotubes. [1]
Counterintuitively, multiwall CNTs (concentric tubes of graphite) are less effective actuators because their solvent accessible surface area is typically lower than that of single walled nanotubes. [1]
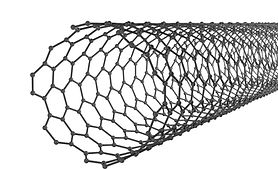

References:
​
[1] John D. W. Madden, Nathan A. Vandesteeg, Patrick A. Anquetil, Peter G. A. Madden, Arash Takshi, Rachel Z. Pytel, Serge R. Lafontaine, Paul A. Wieringa, and Ian W. Hunter. 2004. Artificial Muscle Technology: Physical Principles and Naval Prospects. IEEE Journal Of Oceanic Engineering, 29(3): 706-728
​
[2] Detsi E, Sarah H, Tolbert S, Punzhin, De Hosson JTM. 2016. Metallic muscles and beyond: nanofoams at work. J. Mater. Sci., 51:615–634
​
[3] Drossel WG, Bucht HKA, Weisheit L, Pagel K. 2015. Smart3 – Smart Materials for Smart Applications. 2015. Procedia CIRP, 36: 211 – 216
​
[4] Chu WS, Lee KT, Song SH, Han MW, Lee JY, Kim HS, Kim MS, Park YJ, Cho KJ, and Ahn SH. 2012. Review of Biomimetic Underwater Robots UsingSmart Actuators. International Journal of Precision Engineering And Manufacturing, 13(7) :1281-1292
​
[5] Savannah Swardz. Shape Memory Alloys. Retrieved 23, August, 2017 at https://depts.washington.edu/matseed/mse_resources/Webpage/Memory%20metals/applications_for_shape_memory_al.htm
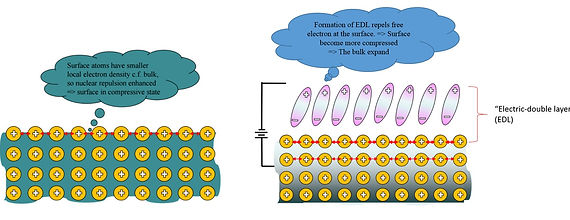