Introduction
This project was carried out at The University of Hong Kong as an undergraduate capstone project under the supervision of Professor Ngan A.H.W. from 2016-2017.
"Natare" means "to swim" in Latin. This project work includes building a micro-robot with the newly developed Nickel hydroxide/oxyhydroxide electrochemical actuator recently publsihed by our lab. The scope of work includes fabricating the actuator with electroplating technique, understanding how the actuator behaves under different conditions, and prototyping the control circuit and body of the micro-robot.
Background - Artificial muscles
Artificial muscles, as its name suggests, are materials that are capable of doing mechanical work by undergoing dimensional changes. Similar to animal skeleton muscles, these materials can stretch and contract, generating displacements ranging from several nanometers to a few meters. Common types of actuating materials include piezoceramics (common material for force sensors), electroactive polymers, and shape memory alloys. Each actuating material possess a different strain and stress characteristics, and is therefore suitable for different real-life applications.
​
On the large scale, artificial muscles may be employed to replace electric motors for actuation, such as motor-driven robotic joints or petrol cap release mechanisms in cars. [1] On a smaller scale, artificial muscles’ can be applied as propellers for meso- or micro-scale robots, or even serve as microvavles in micro-electro-mechanical systems (MEMs), or lab-on-a-chip technology. [2] These enable new propulsion and actuation mechanism in robotics to be developed, saving energy and space.
​
Our lab have been focusing on the development of nanoporous metals, a category of actuating materials with nano-scale surface features. Nanoporous metals have a large surface area to conduct and store electric charges and are often employed as battery electrodes or capacitors. Later it was discovered that these stored electric charges would affect the surface stress of the metal, causing it to deform itself. Nanoporous metals have since become a popular research topic in actuation materials due to the convenience to control its displacement by supplying electricity. The degree of deformation mainly depends on the voltage applied to the material, electric capacity, and the pore density (and thus flexibility) of the metal. Nanoporous metals possess the advantages of low voltage input (requires several volts only, compared to > 1kV for piezoceramics), fast response rate, and relatively high actuation stress (compared to some compliant electroactive polymers). However, one major limitations of nanoporous metals is that it has to be actuated in a wet environment, relying on the ions in the liquid electrolyte to transport electric charges to its surface. The goal of producing nanoporous actuators capable of actuation in a dry environment, along with the hope of achieving higher actuation strain and stress have since been driving the continuous research for nanoporous metals.
​
Kwan [3] from our lab recently discovered that nickel hydroxide thin films undergoes centimeter-scale displacement when it is applied with an alternating voltage (+/- 1.5V) and immersed in 1 M sodium hydroxide (NaOH) solution. When the voltage is alternated at a frequency ~ 1 Hz it generates a flapping motion similar to fishtail as shown in the video below.
References
[1] Drossel WG, Bucht HKA, Weisheit L, Pagel K. 2015. Smart3 – Smart Materials for Smart Applications. 2015. Procedia CIRP 36: 211 – 216
​
[2] Detsi E, Sarah H. Tolbert, S. Punzhin, Jeff Th. M. De Hosson. 2016. Metallic muscles and beyond: nanofoams at work. J. Mater. Sci., 51:615–634
​
[3] Kwan KW, Hau NY, Feng SP, Ngan HW. 2017. Electrochemical actuation of nickel hydroxide/oxyhydroxide at sub-volt voltages. Sensors and Actuators B, 248:657–664
​
​
​
​
​
Motivation
From artificial muscles to micro-robots
Note: The video shows the free locomotion test video in 64 x fast forward speed.
The actuator consist of a two-layer structure, a pure nickel layer of 0.2-0.4 µm acting as the substrate and the actuating layer of nickel hydroxide (Ni(OH)2) of 3-5 µm thick. When a positive voltage is applied to the actuator, nickel hydroxide oxidizes and becomes nickel oxyhydroxide (NiOOH) and is accompanied by a volume expansion. As the actuating layer expands, the actuator bends towards the direction of the substrate layer, putting the substrate under compression. When negative voltage is applied, the volumetric expansion disappears as nickel oxyhydroxide reduces to nickel hydroxide,
relaxing the material back to its neutral position. This reduction-oxidation reaction is sometimes abbreviated as 'redox' reaction, and the actuation caused by reversible volume changes in nickel hydroxide layer is called the redox reaction actuation mechanism.
​
Since the displacement of the actuator almost resembles a fish's tail, and its motion is easily controlled by the applied voltage, it would be interesting to experiment its application potential as a compact prime-mover. The main goal of 'Ni-Natare' project is thus to build a device which can be propelled by the actuator.
Video showing weight-lifting using dielectric elastomers, a kind of artifical muscle.
[Research by Empa - Material Science and Technology - Switzerland]
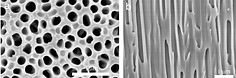
Scanned electron microscopy images of nanoporous metals from top view (left) and side view (right).